Advanced Metal Stamping Methods for Precision Manufacturing
Advanced Metal Stamping Methods for Precision Manufacturing
Blog Article
Releasing the Prospective of Steel Stamping: Expert Tips and Finest Practices Exposed
In the realm of metal stamping, where accuracy and performance preponderate, the mission to maximize processes and unlock surprise potentials is a perpetual quest. Experience developed over years of industry experience, integrated with innovative practices and innovative technologies, holds the vital to achieving exceptional results. As we navigate through the intricate world of steel marking, a better take a look at the complexities of tooling style, product selection, manufacturing performance, quality assurance, and emerging trends promises a treasure chest of understandings waiting to be discovered. Stay tuned to uncover how these expert ideas and ideal practices can change the metal stamping landscape.
Tooling Design Optimization
Enhancing tooling style is essential for improving effectiveness and accuracy in steel marking procedures. A well-balanced tooling design can substantially influence the top quality and cost-effectiveness of steel stamping operations. By meticulously thinking about elements such as material choice, die setup, and component geometry, makers can enhance manufacturing procedures and enhance general product high quality.
One secret element of tooling style optimization is picking the most suitable materials for the dies and punches used in the stamping process. Proper die design can aid stop problems such as wrinkling, tearing, and extreme springback, leading to higher production returns and minimized scrap rates.
Moreover, maximizing component geometry through tooling layout can assist reduce material waste and production time. By thoroughly forming passes away and punches to match the desired component specs, makers can accomplish tighter resistances and boosted component high quality. In general, investing time and resources in enhancing tooling style can result in substantial lasting benefits for steel stamping operations.
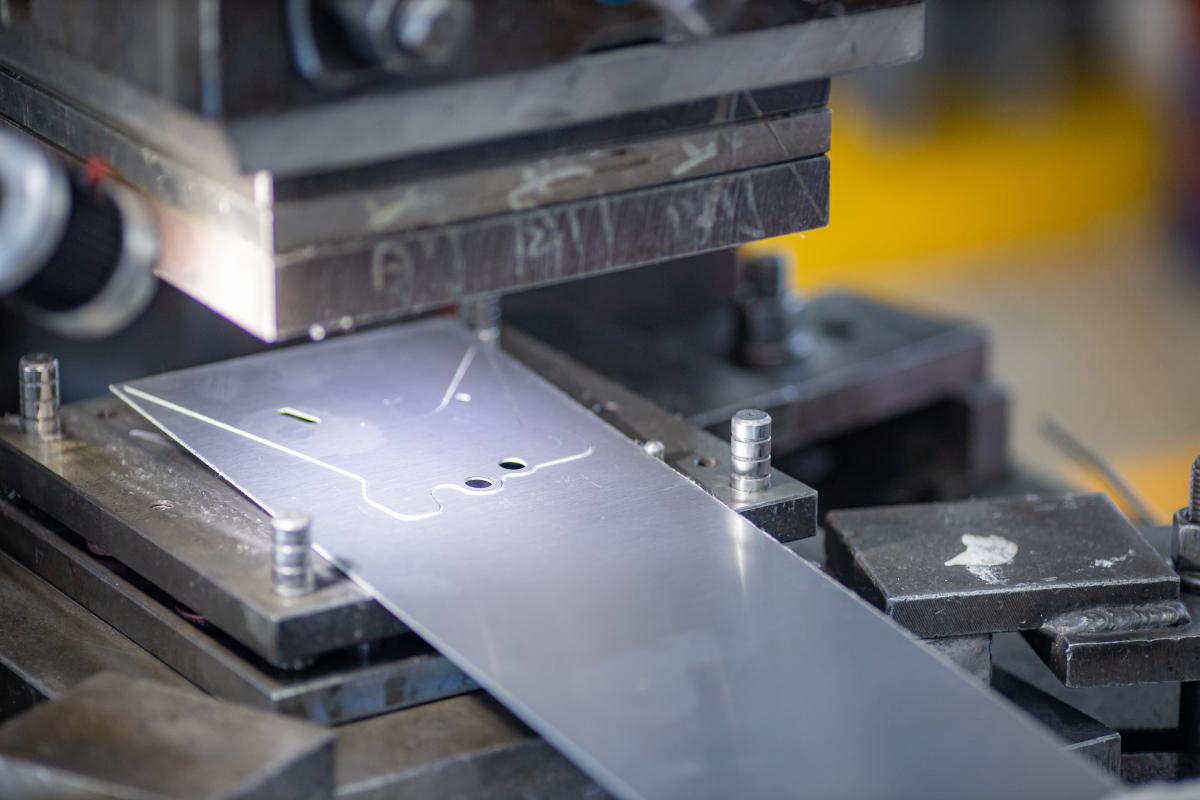
Product Selection Approaches
Tactically picking materials for metal marking tooling is paramount for making sure sturdiness and efficiency in manufacturing processes. When choosing materials for steel stamping applications, numerous essential factors have to be thought about. The very first factor to consider is the sort of material being stamped. Various products, such as light weight aluminum, stainless-steel, or copper, require specific tooling materials to guarantee ideal performance and durability.
Another vital variable in material selection is the expected production volume - Metal Stamping. For high-volume production runs, tooling products with remarkable wear resistance and durability, such as device steels or carbide, are frequently chosen to endure the roughness of continuous stamping procedures
In addition, the complexity of the stamping design and the called for accuracy also play a substantial duty in material selection. For complex stamping patterns or limited tolerances, materials with high thermal conductivity and superb machinability, like beryllium copper or tool steel alloys, may be much more suitable to attain the preferred outcomes.
Manufacturing Effectiveness Strategies
To improve producing result and minimize production expenses, applying efficient techniques in metal marking procedures is crucial. Automated metal stamping equipments can execute tasks with precision, consistency, and at a much faster rate than hands-on labor, leading to boosted performance and lowered cycle times.
An additional technique to boost manufacturing performance is via continual process improvement. Carrying out routine audits Learn More and performance assessments can help identify bottlenecks, ineffectiveness, and areas for enhancement within the metal marking procedure. By analyzing data and feedback from these evaluations, manufacturers can apply targeted options to enhance operations, boost throughput, and make the most of overall performance.
In addition, taking on lean manufacturing principles, such as 5S methodology and Kanban systems, can help remove waste, boost operations, and boost total efficiency in metal marking operations. By fostering a society of continual enhancement and empowering staff members to add ideas for performance gains, producers can open the complete potential of their steel stamping processes.
High Quality Control Measures
Building on the foundation of reliable production techniques in metal marking processes, making sure rigorous quality assurance procedures is necessary for maintaining product requirements and consumer fulfillment. Quality assurance in steel stamping includes organized inspection, testing, and tracking of the production processes to determine and fix any type of inconsistencies or defects that might compromise the end product's stability (Metal Stamping). Carrying out measures such as regular equipment maintenance, in-process assessments, and thorough testing of finished parts can assist discover concerns early on and prevent costly rework or product recalls
Along with aggressive top quality control measures, it is vital to develop clear high quality criteria and requirements that straighten with customer demands. Regular audits and evaluations of high quality processes can assist identify areas for renovation and ensure consistency in item high quality. By promoting a society of top quality awareness amongst workers and supplying ample training on quality assurance procedures, manufacturers can enhance overall product reliability and brand name reputation. Ultimately, buying robust top quality control gauges not only safeguards versus issues and non-conformities but also leads the way for continual business growth and customer loyalty.

Innovative Metal Stamping Technologies
Improvements in steel stamping modern technologies have changed the manufacturing industry, boosting efficiency and accuracy in the production process. One of the most considerable technologies is the development of servo press innovation. Servo presses supply exceptional control over the marking procedure, allowing for adjustments in dwell, rate, and force time with outstanding precision. This degree of control results in higher browse around this web-site high quality components, lowered downtime for tooling adjustments, and raised total productivity.
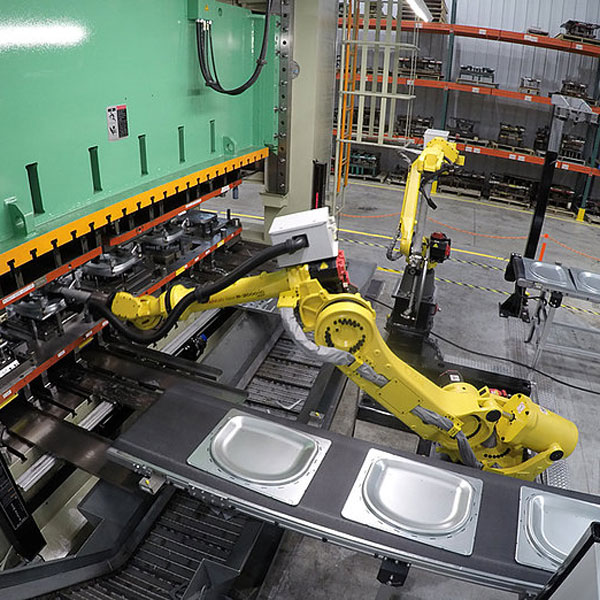
Furthermore, the fostering of additive production techniques in metal stamping, such as 3D printing of die parts, has streamlined the tooling style and production process. This technique permits better layout adaptability, rapid prototyping, and cost savings in tooling production. By leveraging these innovative innovations, makers can open brand-new degrees of performance, top quality, and competition in the steel marking sector.
Verdict
To conclude, the optimization of tooling layout, strategic material selection, efficient production techniques, quality control measures, and innovative innovations are crucial for unleashing the full capacity of metal stamping. By executing these finest methods and skilled tips, producers can enhance efficiency, raise top quality, and remain affordable in the steel marking sector. It is crucial for companies to continuously evaluate and improve their procedures to attain success in this area.
As we browse via the intricate world of metal stamping, a closer look at the complexities of tooling layout, material option, production performance, top quality control, and emerging trends promises a prize chest of understandings waiting to be discovered. A well-thought-out tooling style can significantly influence the top quality and cost-effectiveness of metal marking procedures.Building on the foundation of efficient manufacturing methods in metal stamping procedures, making sure strict quality control actions is imperative for preserving item standards and consumer satisfaction. Quality control in steel stamping entails methodical evaluation, screening, and surveillance of the manufacturing refines to determine and rectify any type of discrepancies or defects that can jeopardize the last item's integrity.In final thought, the optimization of tooling design, critical material option, effective manufacturing techniques, top quality control procedures, and ingenious modern technologies are necessary for letting loose the full potential of steel marking.
Report this page